TPM viết tắt của Total Productive Maintenaince tạm gọi là Bảo trì Năng suất toàn diện. Việc thực hiện TPM là nhằm tối đa hóa hiệu suất thiết bị, nâng cao năng suất với một hệ thống bảo trì được thực hiện trong suốt vòng đời của thiết bị, đồng thời nâng cao ý thức và sự hài lòng với công việc của người lao động. Với TPM, mọi người cùng hợp lực và tương tác với nhau để nâng cao hiệu suất hoạt động của thiết bị một cách hiệu quả nhất. Suy nghĩ trách nhiệm của tôi (công nhân vận hành thiết bị) là vận hành thiết bị, trách nhiệm của anh (công nhân bảo trì) là sửa chữa thiết bị, được thay bằng tôi và anh cùng chịu trách nhiệm về thiết bị của chúng ta, nhà máy của chúng ta, tương lai của chúng ta.
BẢO TRÌ NĂNG SUẤT TOÀN DIỆN – TPM
1. Ba kỹ thuật bắt đầu bằng chữ T
- Hiện nay, cùng với ISO 9000 quản lý chất lượng toàn diện (TQM) đang được nhiều người Việt Nam biết đến.Đây là một trong ba kỹ thuật (đều bắt đầu bằng chữ T) của người Nhật nhằm cung cấp các phương pháp quan trọng để nâng cao hiệu quả sản xuất. Hai kỹ thuật còn lại là TPS (Toyota Production System: hệ thống sản xuất Toyota), còn gọi là JIT (Just – In – time: đúng lúc) và TPM (Total Productive Maintenance: Bảo trì năng suất toàn diện).
- Mục đích của TQM là huy động con người phát huy sáng kiến, cải tiến thường xuyên chất lượng sản phẩm, của TPS/JIT là giảm thời gian sản xuất, giảm dự trữ vật tư tồn kho đến mức tối thiểu, còn TPM là nhằm tăng tối đa hiệu suất sử dụng máy móc, thiết bị với một hệ thống bảo trì được thực hiện trong suốt quá trình tồn tại của máy móc thiết bị. TPM liên quan đến tất cả mọi người, tất cả các phòng ban và tất cả các cấp.Như vậy, có thể hình dung TQM và TPS hướng về phần mềm, còn TPM hướng về phần cứng của hệ thống sản xuất.
- TPM bắt đầu được triển khai ở Nhật Bản từ năm 1971 và đã tạo ra những kết quả mang tính cách mạng về mặt năng suất và chất lượng. Ngày nay TPM đã được áp dụng phổ biến tại nhiều nước phương Tây cũng như Châu Á, đặc biệt là ở Nhật Bản, Hàn Quốc và Trung Quốc.
- Ba kỹ thuật bắt đầu bằng chữ T này được xem là ba công cụ chủ yếu của sản xuất trình độ thế giới (World Class Manufacturing).
2. Sự phát triển của TPM
- Trong những thập niên 1950 và 1960 công nghiệp Nhật Bản đã thực hiện một chương trình xây dựng nhanh chóng các nhà máy và cơ sở sản xuất đạt năng suất cao. Trong khi quá trình này diễn ra, rõ ràng là năng suất và chất lượng sản phẩm trong công nghiệp chịu ảnh hưởng rất lớn bởi tình trạng của các nhà máy và cơ sở sản xuất. Để kiểm soát những yếu tố này, các kỹ thuật bảo trì nhà máy được nhập từ Hoa Kỳ. - Trọng tâm của bảo trì nhà máy là Bảo trì phòng ngừa, sau này được cải tiến thành một phương pháp gọi là Bảo trì năng suất, do Công ty General Electric phát triển nhằm nâng cao năng suất. Bảo trì nhà máy, cùng với cốt lõi của nó là Bảo trì phòng ngừa, đã dẫn đến sự hình thành các tổ chức bảo trì chuyên sâu, xây dựng các hệ thống bảo trì nhà máy và phát triển các công nghệ chẩn đoán. Thông qua các hoạt động nâng cao hiệu quả của công tác bảo trì, bảo trì nhà máy đã góp phần đáng kể vào sự phát triển của công nghiệp Nhật Bản.
- TPM là một chương trình do Viện bảo trì nhà máy Nhật Bản (JIPM) đề xuất và triển khai từ năm 1971. Từ đó đến nay TPM đã có những bước tiến bộ vượt bậc, là động lực chủ yếu thúc đẩy sự gia tăng năng suất và sự thành công của công nghiệp Nhật Bản. JIPM xem TPM là biện pháp có hiệu quả nhất, chắc chắn nhất để Sản xuất đạt trình độ thế giới. Các hội nghị “Sản xuất đạt trình độ thế giới và JIPM-TPM “đã được tổ chức tại Paris lần đầu tiên vào tháng 7/1997.
- Hiện nay TPM được áp dụng với một qui mô ngày càng rộng rãi trong các lĩnh vực như TPM văn phòng và TPM kỹ thuật, đồng thời giá trị của nó cũng vươn dài ra từ bảo trì đến quản lý.
- Rõ ràng là “ngày nay TPM là một kỹ thuật lý tưởng để thúc đẩy và đảm bảo Sản xuất trình độ thế giới” (Tokutaro Suzuki, Phó chủ tịch Viện Bảo trì Nhà máy Nhật bản).
3. Định nghĩa bảo toàn năng suất toàn diện
Bảo trì năng suất toàn diện được định nghĩa ngắn gọn như sau:
Bảo trì năng suất toàn diện được định nghĩa ngắn gọn như sau:
- TPM là bảo trì năng suất được thực hiện bởi tất cả các nhân viên thông qua các nhóm hoạt động nhỏ.
- Trong phương diện này TPM nhìn nhận rằng các tình huống bảo trì khác nhau trong một công ty có thể cần nhiều phương pháp khác biệt để thực hiện có hiệu quả một giải pháp, những giải pháp này có thể thay đổi từ máy này đến máy kia hoặc từ nhà máy này đến nhà máy kia. Nhiều kỹ thuật dùng trong TPM không mới mẻ gì, cái mới là văn hóa Nhật Bản đã xâm nhập vào TPM với sự tham gia của toàn bộ công nhân viên và sự liên kết giữa các nhóm hoạt động nhỏ.
- Những đóng góp quan trọng của TPM vào lý thuyết bảo trì là nó đã phá bỏ rào cản hoặc ranh giới giữa bộ phận bảo trì và bộ phận sản xuất trong một công ty. Một tư tưởng về “chúng tôi tạo dựng, các anh đập đổ ” đã bị loại bỏ hoàn toàn khi TPM được áp dụng có hiệu quả. Việc này đã mang lại những lợi ích khổng lồ trong sản xuất và trong công ty của họ.
- Thêm vào đó về phương diện cải tiến liên tục, TPM đã loại bỏ sự tự mãn trong một tổ chức, thay vào đó là một ý thức cao về mục tiêu. Mục tiêu đó là những cố gắng để đạt đến số lần hư hỏng của thiết bị bằng không. Vì vậy năng suất, chất lượng sản phẩm và khả năng sẵn sàng của thiết bị đạt giá trị tối đa.
- Trong phương diện này TPM nhìn nhận rằng các tình huống bảo trì khác nhau trong một công ty có thể cần nhiều phương pháp khác biệt để thực hiện có hiệu quả một giải pháp, những giải pháp này có thể thay đổi từ máy này đến máy kia hoặc từ nhà máy này đến nhà máy kia. Nhiều kỹ thuật dùng trong TPM không mới mẻ gì, cái mới là văn hóa Nhật Bản đã xâm nhập vào TPM với sự tham gia của toàn bộ công nhân viên và sự liên kết giữa các nhóm hoạt động nhỏ.
- Những đóng góp quan trọng của TPM vào lý thuyết bảo trì là nó đã phá bỏ rào cản hoặc ranh giới giữa bộ phận bảo trì và bộ phận sản xuất trong một công ty. Một tư tưởng về “chúng tôi tạo dựng, các anh đập đổ ” đã bị loại bỏ hoàn toàn khi TPM được áp dụng có hiệu quả. Việc này đã mang lại những lợi ích khổng lồ trong sản xuất và trong công ty của họ.
- Thêm vào đó về phương diện cải tiến liên tục, TPM đã loại bỏ sự tự mãn trong một tổ chức, thay vào đó là một ý thức cao về mục tiêu. Mục tiêu đó là những cố gắng để đạt đến số lần hư hỏng của thiết bị bằng không. Vì vậy năng suất, chất lượng sản phẩm và khả năng sẵn sàng của thiết bị đạt giá trị tối đa.
Định nghĩa đầy đủ hơn của bảo trì năng suất toàn diện bao gồm :
- Mục tiêu tối đa hóa hiệu quả của thiết bị sản xuất về mặt hiệu suất kinh tế và khả năng sinh lợi.
- Thiết lập một hệ thống bảo trì sản xuất xuyên suốt bao gồm công tác bảo trì phòng ngừa, cải thiện khả năng bảo trì và bảo trì phòng ngừa cho toàn diện chu kỳ sống của một thiết bị.
- Thực hiện bảo trì năng suất trong công ty bởi tất cả các phòng ban tương ứng.
- Sự tham gia của tất cả những thành viên trong công ty từ lãnh đạo đến công nhân tại phân xưởng trong việc áp dụng bảo trì năng suất.
- Xúc tiến bảo trì năng suất thông qua các hoạt động nhóm bảo trì nhỏ tự quản.
- Bảo trì năng suất toàn diện là một chiến lược bảo trì làm nền tảng cho sản xuất, nâng cao chất lượng sản phẩm và giảm chi phí.
4. Triết lý của TPM
- TPM nhằm mục tiêu tạo ra một hệ thống phối hợp làm cực đại hiệu suất của hệ thống sản xuất (nâng cao hiệu suất toàn diện).
- TPM hình thành các hệ thống phòng ngừa những tổn thất xảy ra trong sản xuất và tập trung vào sản phẩm cuối cùng. Các hệ thống này nhằm đạt được “không tai nạn, không khuyết tật, không hư hỏng” trong toàn diện chu kỳ hoạt động của hệ thống sản xuất.
- TPM được áp dụng trong toàn diện các phòng, ban, bộ phận như thiết kế, sản xuất, phát triển và hành chánh.
- TPM dựa trên sự tham gia của toàn diện các thành viên, từ người lãnh đạo cao nhất đến các nhân viên trực tiếp sản xuất.
- TPM đạt được các tổn thất bằng không thông qua hoạt động của các nhóm nhỏ
5. Ba ý nghĩa của chữ toàn diện (T) trong TPM
- Hiệu suất hoạt động toàn diện.
- Hệ thống hóa toàn diện.
- Sự tham gia của toàn diện các thành viên
6. Những mục tiêu của TPM :
- Tăng hiệu suất và năng suất.
- Giảm khuyết tật và hư hỏng.
- Giảm chi phí sản xuất và bảo trì.
- Tinh thần và thái độ làm việc của mọi người tích cực hơn.
- An toàn lao động cao.
- Thời gian ngừng sản xuất ngắn nhất.
- Không có ngừng máy ngoài kế hoạch.
- Phát triển và đào tạo kỹ năng cho nhân viên.
- Cải tiến liên tục môi trường làm việc.
Vì vậy TPM có một mục tiêu chính là tối đa hiệu quả của thiết bị trong một công ty, và để làm điều đó, trách nhiệm trực tiếp thuộc về người sử dụng thiết bị. Trong việc nổ lực hướng đến mục tiêu này, TPM cung cấp một phương án chặt chẽ đối với các công ty sử dụng thiết bị. Trong bối cảnh này TPM có thể được nghĩ đến như là một áp dụng thực tiễn bảo trì tốt nhất.
7. Mười hai bước thực hiện TPM
Để thực hiện TPM cần 12 bước, được chia thành 4 giai đoạn:
- Giai đoạn chuẩn bị.
- Giai đoạn giới thiệu.
- Giai đoạn thực hiện.
- Giai đoạn củng cố.
Giai đoạn chuẩn bị : từ 3 đến 6 tháng, gồm các bước:
- Bước 1 : Lãnh đạo cao nhất giới thiệu TPM.
- Bước 2 : Đào tạo và giới thiệu TPM.
- Bước 3 : Hoạch định các tổ chức tiến hành thực hiện TPM.
- Bước 4: Thiết lập các chính sách cơ bản và các mục tiêu của TPM.
- Bước 5: Trình bày kế hoạch phát triển TPM.
Giai đoạn giới thiệu TPM :
- Bước 6: Bắt đầu TPM (hoạch định và thực hiện).
Giai đoạn thực hiện:
- Bước 7: Cải tiến hiệu suất của mỗi thiết bị trong dây chuyền sản xuất.
+ Xác định rõ công việc.
+ Xem xét tình trạng máy móc.
+ Xem xét mối quan hệ giữa máy móc, thiết bị, vật tư và các phương pháp sản xuất.
+ Xem xét trình tự đánh giá chung.
+ Xác định cụ thể các vấn đề.
+ Đề xuất các cải tiến phù hợp.
- Bước 8: Tổ chức công việc bảo trì.
+ Chuẩn bị.
+ Đo lường, kiểm tra dựa vào các nguyên nhân.
+ Thiết lập tiêu chuẩn làm sạch và bôi trơn.
+ Kiểm tra tổng thể.
+ Kiểm tra việc tự quản.
+ Đảm bảo tính ngăn nắp và gọn gàng.
+ Đảm bảo tính ngăn nắp và gọn gàng.
+ Tự quản lý hoàn toàn.
- Bước 9: Thực hiện công việc bảo trì có kế hoạch trong bộ phận bảo trì.
- Bước 10: Đào tạo để nâng cao các kỹ năng bảo trì và vận hành.
- Bước 11: Tổ chức công việc quản lý thiết bị.
Giai đoạn củng cố:
- Bước 12: Thực hiện hoàn chỉnh TPM ở mức độ cao hơn.
8. Lean TPM
- Lean và TPM được kết hợp để hình thành Lean TPM.
- Lean TPM nếu được thực hiện đúng, không chỉ mang lại hiệu quả mà còn làm tăng năng suất và giảm các loại lãng phí.
- Lean TPM đòi hỏi một tổ chức tập trung vào các chức năng bảo trì và kỹ thuật để cải thiện thời gian máy chạy, khả năng sẵ khả năng sẵn sàng và chát lượng. Làm được như vậy các đội bảo trì được tăng cường tri thức về thiết bị đồng thời phát triển mối quan hệ thân thiện và tích cực giữa họ với nhau và với các bộ phận khác trong doanh nghiệp.
- Mục tiêu của Lean TPM là hình thành một đội ngũ bảo trì tạo ra giá trị gia tăng mà không làm tăng chi phí trong phạm vi doanh nghiệp.
- Phần lớn doanh nghiệp đều biết nhưng không thể hiểu đến nơi đến chốn các thiệt hại ẩn gây ra do ngừng máy, những lần gián đoạn sản xuất để thay đổi đồ gá hoặc điều chỉnh máy, tốc độ máy bị giảm, máy chạy không hoặc ngừng vài phút, khởi động lại, sản phẩm khuyết tật và công việc tái chế.
- Vì vậy nguyên tắc chính của một chương trình lean TPM là hiểu, định lượng và tiến hành làm giảm đến mức tối thiểu hậu quả của những thiệt hại nêu trên.
9. Thực hiện Lean TPM
Mức 1: Ổn định hóa
Mức 1A: Kiểm soát
- Phân tích tình trạng hiện thời của thiết bị. Làm vệ sinh toàn bộ khu vực sản xuất.
- Hoàn thành việc đánh giá và xác định tầm nhìn, mục tiêu.
- Bắt đầu ghi nhận các chỉ số hiệu năng của thiết bị và nhận dạng tiềm năng cải thiện.
Mức 1B: Ổn định hóa
- Thực hiện kế hoạch bảo trì hàng năm và phát triển thêm chương trình bảo trì có kế hoạch.
- Xác định lộ trình cải tiến và phân công trách nhiệm cải tiến các tiêu chuẩn, định mức.
- Khẳng định tầm nhìn và mục tiêu. Lập tài liệu và truyền thông cho mọi người có liên quan.
- Bắt đầu thực hiện các qui trình bảo trì phòng ngừa.
Mức 2: Tối ưu hóa
Mức 2A: Tinh gọn từ thực tế
- Phát triển chương trình để tăng mức độ bảo trì trên cơ sở tình trạng.
- Cải thiện môi trường vận hành thiết bị.
- Phấn đấu giảm số lần hư hỏng máy.
Mức 2B: Nhắm mục tiêu số hư hỏng bằng không
Phát triển một chương trình bảo trì chất lượng nhằm đạt mục tiêu số hư hỏng máy và số sản phẩm khuyết tật bằng không.
10. Kết luận
TPM và Lean TPM còn rất xa lạ với đa số các doanh nghiệp sản xuất công nghiệp Việt Nam trong khi bảo trì vẫn là công việc hàng ngày phải làm. Vì mục tiêu giảm thiệt hại tối đa do ngừng máy, đã đến lúc các doanh nghiệp cần tăng tốc trong việc áp dụng các hệ thống quản lý bảo trì tiên tiến mà TPM có thể là mục tiêu trước mắt.
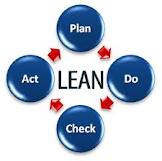
Lean Manufacturing, còn gọi là Lean Production, là một hệ thống các công cụ và phương pháp nhằm liên tục loại bỏ...
.jpg)
Thông thường mỗi chức danh sẽ có bản mô tả công việc hoặc kế hoạch làm việc hàng tháng. Nhà quản lý sẽ áp...
.jpg)
Sau chiến tranh thế giới thứ hai, nước Nhật phải đối mặt với muôn vàn khó khăn, hiệp hội các nhà khoa...
« Trước Tiếp »